Minor courses of study don’t get enough praise. I’m currently minoring in business administration and space studies to complement my Communication degree. My initial intention was to take something I was interested in that was sensible for my field, and they certainly are, but I didn’t recognize the true value of them until working with Space Tango.
Space Tango works to scale down customers’ experiments to fit in what they call CubeLabs for microgravity research on the International Space Station. As a Communication major, it’s difficult to see how I piece into this puzzle of research and design. My minor, however, in space studies (SP) provides me with the background information to keep up with the engineers during our meetings. It’s a puzzle piece to the bigger picture.
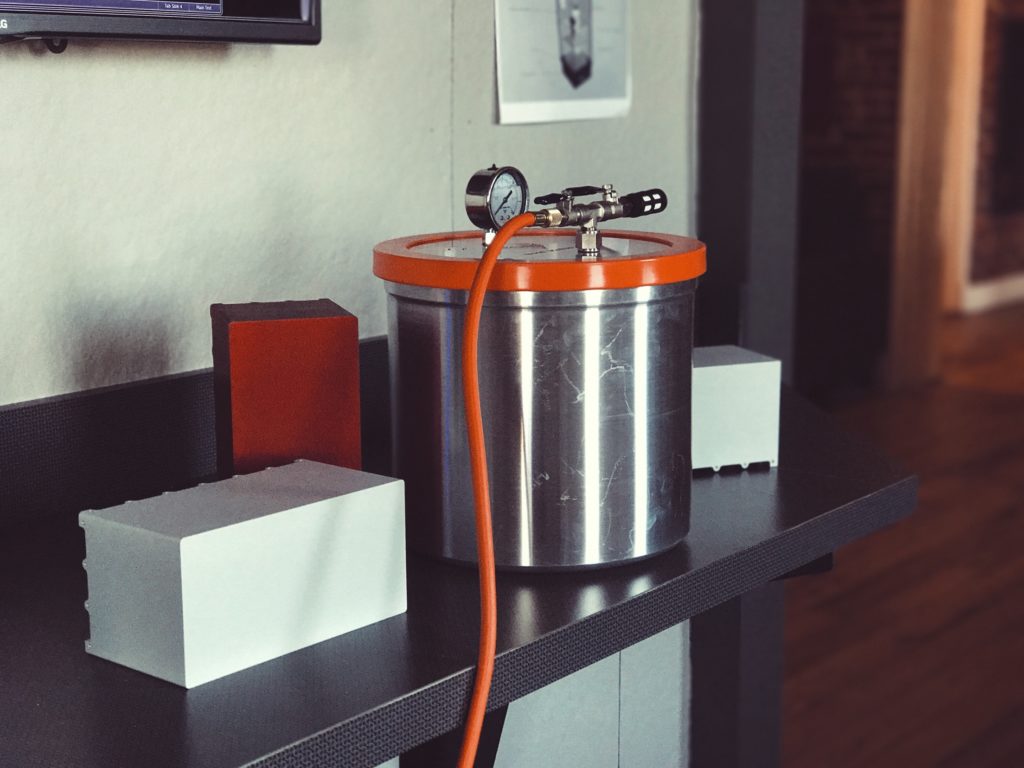
CubeLabs waiting to be tested in a pressure chamber.
SP courses that I have taken gave me an overview of mission history, rocket and propulsion systems, ISS configuration, and so much more. If it wasn’t for my SP minor, then I wouldn’t be as valuable as I am now in the aerospace industry and I wouldn’t be able to effectively market their brand to prospective customers.
My business minor ties it all together. I can keep up with our director of business operations and even devise my own marketing plans that reflect the industry and the company. It’s like being a triple threat in the job market. I have so much more to offer as an intern and, one day, as an employee.
My skills are flexible and it’s all thanks to my minors! I think finding such minors are especially beneficial for flexible degree programs such as Communication. We can fit anywhere, but if there’s an industry you want to work in then cater your education towards it. Especially during internship season and applications, it’s important to keep a few things in mind. What are your strengths? What sets you aside from others? Don’t overestimate the power of your minors. Take the time to find one or two that accommodates your interests or pieces you into your dream industry.
⋆ Dani